Partial Discharge: Causes and Classification by Physical Characteristics
Partial discharge (PD) is an incomplete discharge that bridges the gap between two high voltage electrodes, usually occurring at points where the electric field is concentrated or the insulation material is degraded. This is an early sign of insulation degradation, which can potentially damage equipment if not detected and treated promptly.
Contents
This phenomenon can occur in many locations within the device, including air gaps, the surface of insulating materials, or within microscopic defects in solid insulation. Each discharge medium has different physical characteristics, leading to a classification into four main groups: void discharge, surface discharge, gap discharge, and discharge in liquid or mixed conditions. Each type carries its own formation mechanism and different failure rate.
The common characteristic of partial discharge is that it may be very small and difficult to detect at first, but repeated at high frequency will cause cumulative damage. Over time, these discharge points can become major fault centers, causing insulation breakdown, serious equipment damage or dangerous arc outbreaks. Therefore, monitoring and evaluating partial discharge is not only important for maintenance work but also a key factor in ensuring the safety of the entire operating system.
Classification of partial discharge according to the characteristics of generation
In the actual operation of medium and high voltage equipment, partial discharges can manifest themselves in many different forms depending on the location and environment in which they are formed. Each type has its own generation mechanism and different levels of impact on the insulation system.
One of the most common forms is corona discharge, which occurs when electric charge concentrates at sharp points on the surface of metal or conductors and disperses into the surrounding air. This is a phenomenon that creates a hissing sound or radio interference commonly found in high voltage power systems. Although easily recognizable, corona discharges rarely cause serious damage or affect the safety of equipment.
Arc discharge is a more destructive form of discharge, which occurs when there is a breakdown of the dielectric, resulting in the continuation of an electric current through an ionized gas or insulator. When it occurs, arc discharge can lead to major material losses, fire and explosion, and directly affect the safe operation of the system.
Surface discharge is a phenomenon in which an electric current flows through a thin layer of air on the surface of an insulating material. This type of discharge often occurs in areas with dust, moisture or harsh environmental conditions. In medium and high voltage equipment, surface discharge is a major cause of rapid deterioration of insulation quality, especially when the surface is not properly maintained.
Void discharges typically occur within solid insulating materials where air pockets, defects or non-uniform gaps exist. This type of discharge tends to develop silently but continuously, causing galvanic corrosion and leading to serious deterioration of the insulating properties of cables, connectors or switching devices. If not detected early, void discharges can expand to full breakdown, leading to serious failure.
Detection and handling of partial discharge in actual operation
Among the forms of partial discharge, surface tracking and void discharge are considered the most serious, especially in medium and high voltage systems. These two forms often develop silently but have the potential to significantly destroy the insulation system and equipment.
The impact of partial discharge, if not controlled promptly, can lead to serious consequences. Prolonged downtime, material loss due to fire and explosion, reduced insulation life and system overload are common risks. The level of impact does not stop at property damage but also directly threatens operational safety and the health of workers.
Currently, there are many methods used to detect partial discharges, such as ultrasonic measurements, radio frequency signal analysis, or ultraviolet radiation detection. However, most of these techniques require the user to be close to the equipment, cannot be applied remotely, or are limited by the material of the enclosure. Implementation requires high skill, extensive training, and does not always ensure the accuracy needed to make timely maintenance decisions.
One advanced solution today is the FLUKE FLK-II910 Precision Acoustic Imager which incorporates exclusive SoundSight™ technology. This device converts ultrasonic signals into visual images, allowing operators to accurately identify the location of discharges without physical contact with the device. The Fluke ii910 requires no complicated accessories, is easy to use out of the box, and provides both visual and audio data for detailed analysis and reporting. It is an effective tool to increase safety, reduce inspection time, and improve reliability in high voltage maintenance work.
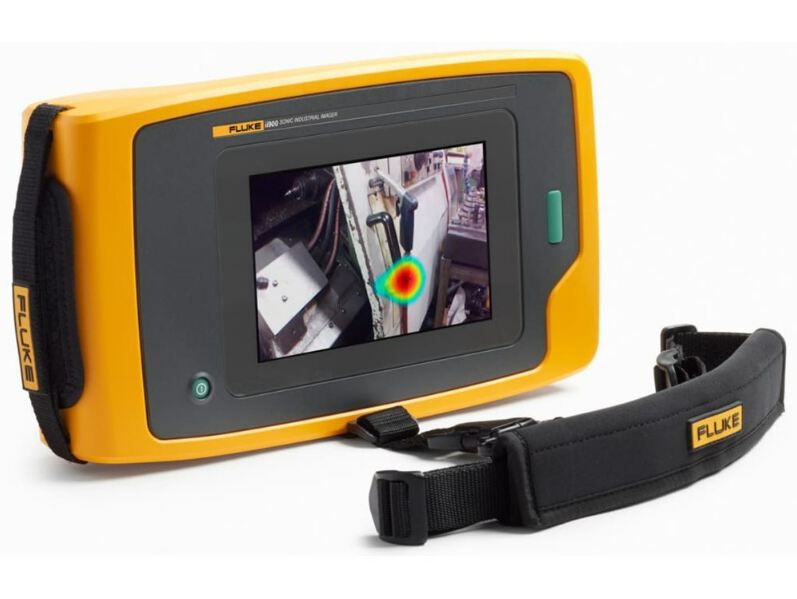