Weld thick iron with a stick welder to make the weld beautiful
As you know, iron is a popular metal today, widely used in life, from making doors, railings, tables and chairs to fences and many other products. Therefore, welding thick iron becomes an indispensable job, especially when it is necessary to ensure durability and sturdiness for processed products. Therefore, thick iron welds need to be done carefully, not only to meet quality requirements but also to ensure penetration and aesthetics.
Contents
Why should you choose a stick welding machine to weld thick iron?
Stick welders are mainly designed for welding metals such as iron, not suitable for special metals such as aluminum, copper or Titanium. This is the reason why stick welding machines become the top choice in processing thick iron.
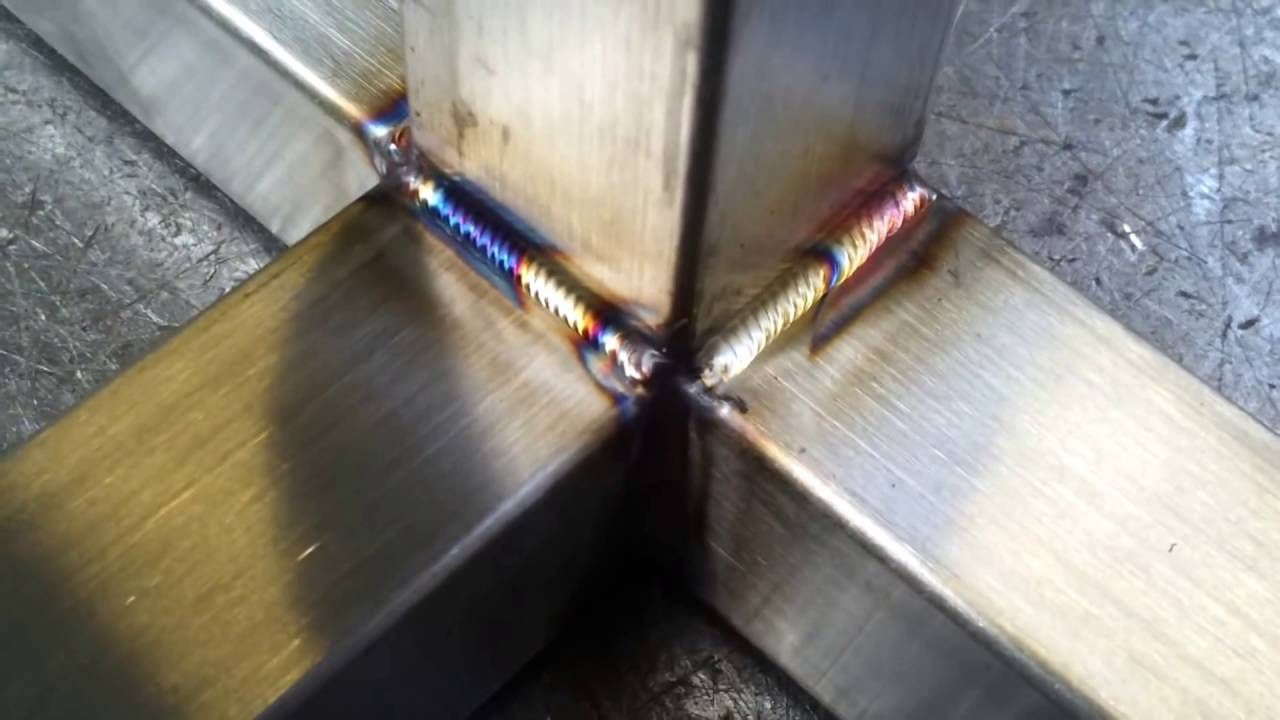
The highlight of the stick welding machine is its reasonable price, lower than that of the Tig or Mig welding machine, but still meets the requirements for beautiful, sturdy welds and guaranteed penetration. Thanks to these advantages, stick welding machines are currently most commonly used in iron welding workshops
For factories that specialize in stainless steel processing or have more diverse needs, they often choose Tig welding machines or multi-purpose machines that integrate both stick and Tig welding to ensure the job. For workshops that only specialize in iron welding, choosing a stick welding machine with appropriate capacity will depend on the nature and specific requirements of each job.
Instructions on how to solder thick iron to standards
Adjust the current when welding thick iron
There is no fixed number for welding current, as this depends on the welding machine you use and the stability of the power source at work.
For example, if the 220V power source is stable and strong, can reach 240V - 250V, you can set the welding current to about 100A for a 200A welding machine. However, if the power source is weaker, only about 200V or even 180V, keeping the welding current at 100A will make the welding process difficult and the weld will not reach the desired quality..
When welding with thick iron, you should adjust the welding current to about 100 - 120A. If the power source is strong, reduce the welding current to avoid welding; If the power source is weak, increase the welding current to ensure a strong and seamless weld. Avoid setting the welding current too low, as this will cause the weld to not penetrate sufficiently. At the same time, do not set the welding current too high because it will damage the weld.
Reference: JASIC ARC 200 JASIC stick welding machine (R04)
Standard welding rod angle when welding thick iron
Method 1: Solder round dots
This method is suitable when soldering iron about 10mm thick. You should place the welding rod at an angle of about 80 degrees to do this. This technique helps the weld focus on one point, ensuring penetration and stability.
Method 2: Welding and pulling
When drag welding to create long straight lines, it is necessary to set a weaker welding current than dot welding to avoid bad or uneven welds.
The ideal welding rod angle for this method is 45 degrees.
- If you want a big, thick weld, you need to pull slowly and evenly.
- If you want a thinner weld, pull faster but still hold steady to ensure a beautiful weld.
Method 3: Weld to create flat joints
This is a technique for those who want a smooth, flat weld that can be further processed by grinding without reducing strength.
To achieve this weld, it is necessary to create a wider gap between the two parts to be welded, allowing the weld puddle to flow deep down and adhere tightly inside. This method ensures a flat and strong weld, unlike methods 1 and 2, where grinding the weld can lose its original strength..
Important notes when soldering thick iron
When welding thick iron, using the overlapping welding technique not only helps the weld achieve stability but also increases aesthetics. Below are some common cases when stacking welding:

Case 1: Overlay welding or overlapping welding with two welded parts placed perpendicularly. This method ensures tight welds, suitable for details that require high durability.
Case 2: Overlapping welding with two welding objects located horizontally. Three different welding styles can be applied depending on the requirements, making the weld more even and beautiful..
Case 3: Horizontal welding with two welding parts placed on the vertical axis. When performing, it is necessary to pay attention to adjusting the welding rod angle appropriately, especially when welding in the horizontal position, so that the weld achieves the best penetration.
Choosing the right technique and adjusting the welding rod angle will help you create welds that are both sturdy and aesthetically pleasing.